When a crisis arises, so do many additional problems leaving people and organizations left scrambling, trying to adapt and picking up the pieces. Take the extreme shortage of personal protective equipment (PPE) gear for healthcare professionals fighting the deadly COVID-19 virus. Before the pandemic struck, no one could have imagined the repercussions of facing an unprecedented crisis such as this, and now with the effects of the virus in full swing, organizations have been stepping up to help numb the pain any way they can.
That includes Philadelphia-based elite athletic apparel manufacturer, Boathouse, who has made the switch to start producing PPE for healthcare professionals. The performance outwear company has been around for over three decades and at this point, the company is used to having to pivot its production to fit current needs. The company started by John Strotbeck originally was geared towards rowers, but over the years has shifted to producing gear for virtually all sports (even Quidditch) and has even been manufacturing side-line apparel for all NFL teams since 1994.
Boathouse saw the desperate need for protective gear for those working on the front lines, and being a company that works quickly and swiftly, they shifted their core competency for producing elite material at a rapid speed. That decision had to be made just as quickly when their entire market closed with the cancellation of all college and high school spring sports and the suspension of all major league sports.
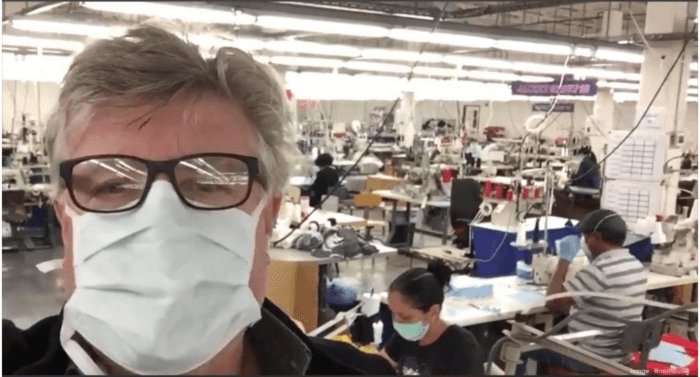
“We had to come up with a strategy to operate at about 50% capacity to get us through the summer so we could survive,” says Strotbeck. “We began to strategize how to do the right thing from our perspective to help fight this virus. Knowing what a skilled manufactury we are and how quickly we can do things, we felt like we could get stuff into the front lines faster than anybody. I had discussions with some friends who were nurses in New Jersey and New York and asked them, what’s needed most? The answer was masks for doctors and nurses because there is a critical shortage.”
Strotbeck—who knows the ins and outs of the apparel game better than most—explained that the reason for the shortage comes down to the fact that supply chains simply can’t handle massive and sudden increases in demand due to the process in which things are made, starting with companies that provide materials. To get things moving quickly, Boathouse had to get a bit creative.
“The same two nurses had a brilliant idea to use existing materials that are sitting in hospitals that are currently being unused,” says Strotbeck. “These materials are known as surgical wraps or surgical filters, and since surgeries are down 80% since COVID started, these materials are just sitting and being unused. So we got some surgical filters from a local hospital, made some prototypes, and sent it back to them—they approved them the same day. The next day we picked up 31,000 of these surgical wraps and we started delivering them the next week in pallets, which is about 10,000 masks. Since then, we’ve picked up material to produce up to 150,000 masks and we’ve delivered at least 30,000 so far.”
Boathouse also has shifted to making gowns with Jockey, who has been working closely with the Encompass Group and the Federal Emergency Management Agency (FEMA). Jockey recently announced its incentive to supply health care workers on the front lines with critically needed Tier 3 Isolation Gowns, and they needed a domestic capacity that could move quickly—enter Boathouse.
“[Jockey] shipped us 10 machines and 300,000 yards of surgical gown material. We went into production with the goal of producing 40,000 to 50,000 surgical gowns in a week,” says Strotbeck.
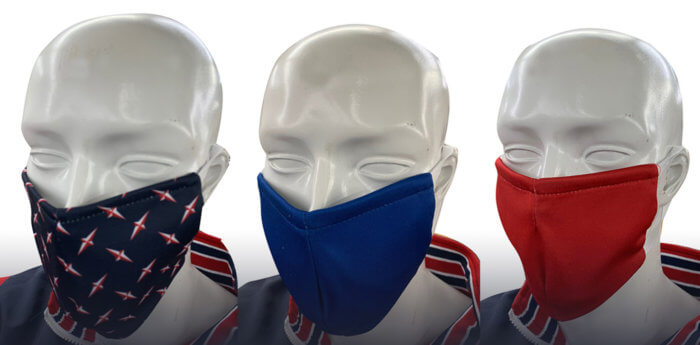
Boathouse has also been able to use some of its own inventory to produce cloth masks, which are not medical-grade, but are in high demand for those who do not work in healthcare. The elite apparel company has even made a deal with Wawa to produce 50,000 masks for their workers over the next four weeks.
The need for these supplies is paramount, but this has also offered a way for Boathouse to get its employees back to work and ultimately help the economy. The company is looking for more help, and for some cases, sewing experience is not required. Although Strotbeck does acknowledge the “valid” fear of the coronavirus, “We have a very controlled environment in our factory, so we make sure everybody comes in wearing gloves and wearing masks, surfaces are getting cleaned twice a day and everybody is staying apart.”
What has been made immensely clear during these times is the shift in people’s priorities, it’s inevitable—but that doesn’t make the process any easier.
“I don’t see this changing for eight weeks at least. We’ve been getting calls from states—Michigan, Maryland, Nevada, California, people are really scrambling to get PPE for their medical people,” says Strotbeck. “The painful thing from a business stand-point, as much as we’re doing, we might be generating 20-25 percent of what our normal revenue typically is here.”
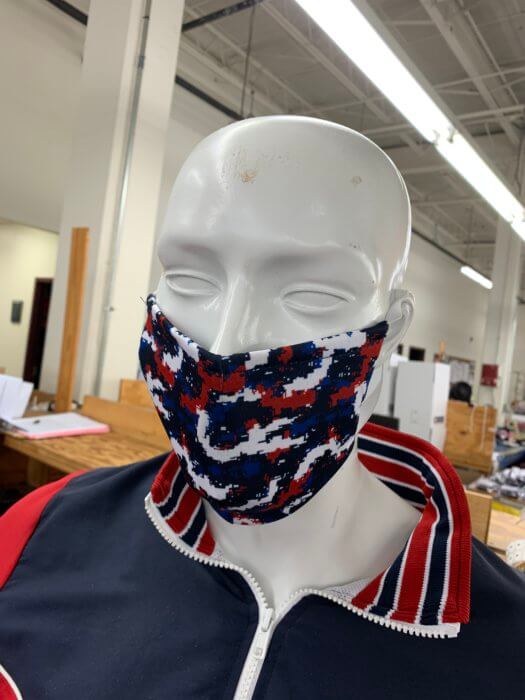
The pain many are feeling is real—but does that mean the absolute worst for businesses? From an organization stand-point, the solutions that establishments have come up with to not only help the crisis but also to save their own business shows, if anything, the adaptation and strength of the human spirit. Strotbeck himself says it best: “I’ve been doing this for 30 years, I’m not going to give it up to a microscopic virus.”
To learn more about Boathouse and its efforts, visit boathouse.com.