Twenty-two 3D printers run 24/7 at the Pennovation Center, a small business incubator developed by the University of Pennsylvania on the banks of the Schuylkill in Grays Ferry.
Businesses in Philadelphia have been shuttered for nearly a month, but production hasn’t stopped inside the facility — it’s changed.
A group of mostly recent Penn graduates and entrepreneurs have set up a 3D printing farm at the center to produce face shields for healthcare workers treating patients with the novel coronavirus.
They started off making 20 or 30 shields a day, and they’re now up to 400 to 500. By the end of the week, Project Shields, the name for their initiative, hopes to produce thousands of shields every day.
Michael Wong spends 16 to 20 hours a day overseeing the process. Sometimes, he naps beside the printers.
His start-up, InstaHub, which makes snap-on automation devices to help property owners eliminate energy waste, is based at the Pennovation Center and uses 3D printing technology. He learned how others were using their printers to fill a gap in personal protective equipment.
“I followed coronavirus news pretty closely,” Wong said. “Then, I saw that there’s this 3D printing community. There’s an explosion of 3D printing face shields and masks.”
It’s a needed explosion. Project Shields, which has been up and running for less than two weeks, has already seen about 10,000 requests for PPE, mostly from hospitals and healthcare workers, but also from smaller clinics and nonprofits that serve the city’s homeless population.
Last month, Wong halted his InstaHub production and focused his resources on making shields. Plastic sheets are cut and hole-punched, and the printers are used to create the headband portion of the shield.
They’re no substitute for N95 masks, which provide the most protection against the coronavirus, but they can help.
“The face shields are definitely not meant to replace the N95 masks,” Evan Weinstein said. “They can be used over top of them, which actually extend the life of the N95 masks that, as I’m sure you know, are in very short supply.”
Weinstein put a pause on his start-up Coco Press, which has been working to develop a 3D printer that prints chocolate, to join Project Shields. He’s donated filament rolls, which are used in the printing process, including some he received as a Christmas gift.
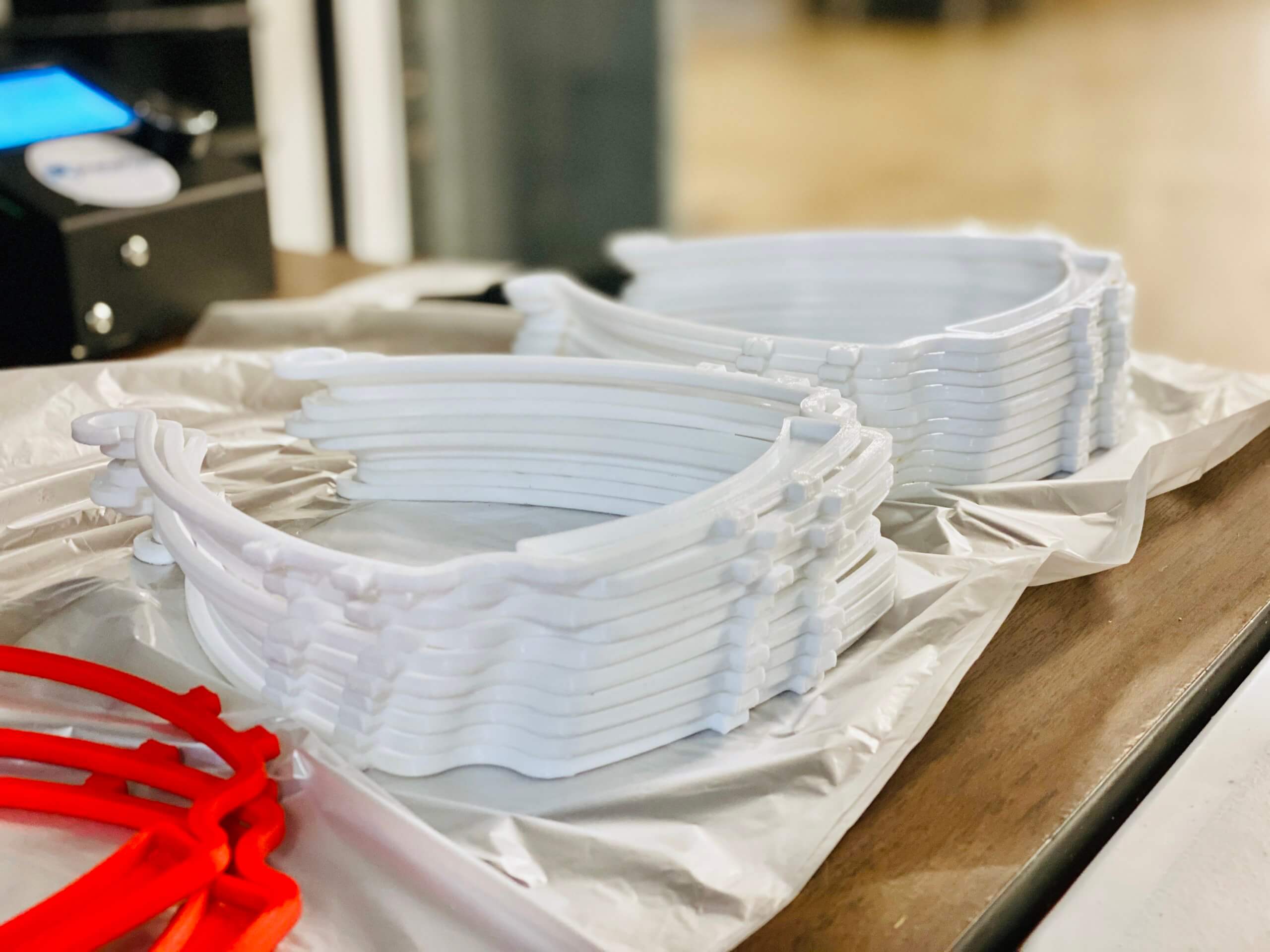
The shields, Weinstein added, also protect the eyes and other parts of the face, and may also prove useful for those who don’t work in a hospital setting, such as grocery store employees and transit workers.
John Gamba, Penn’s entrepreneur-in-residence, and Tiffany Yau, whose organization, Fulphil, teaches entrepreneurial skills to high school students, are the two other members of the Project Shields team.
Yau, who has been the group’s marketing and fundraising guru, was thinking of her father when she decided to contribute to the project. He is a doctor who works in several hospitals with COVID-19 patients in California.
“When (Wong) told me about this, I think it just really hit home,” she said.
The project’s GoFundMe quickly exceeded its initial goal of $25,000 and has so far garnered more than $78,000 with a target of raising $100,000. Yau is also working to procure major gifts and set up corporate matching programs.
Some of that money has gone toward purchasing new 3D printers. InstaHub already had 10, and they have been able to buy 12 more.
Wong said their goal is to produce the shields at a cost of a dollar or less, so they can send as many out as possible. Through Sunday, the group had made about 2,400 shields.
This week, Weinstein said, they should be able to start making additional shields through using injection moulding to create the headbands. It takes about 10 seconds, as opposed to 45 minutes for 3D printing, he said.
Weinstein predicts the new method will allow them to make about 2,500 shields a day.
In addition, he’s reaching out to other companies and people that have 3D printers sitting idle to see if they would be willing to use them to print shields.
For the most part, recipients have picked up their shields from the Pennovation Center, though Project Shields has shipped supplies to other areas hit hard by the virus, including New Jersey and New York.
Organizations and healthcare workers who want shields can visit www.projectshields.org to put in a request.
A small team of volunteers assembles the shields, and several people have signed on to help remotely through marketing and promotion. Additional volunteers are welcome, and those interested can visit the website.